
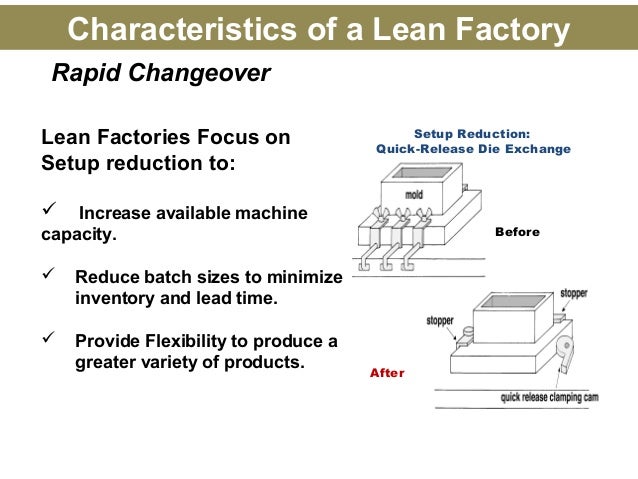
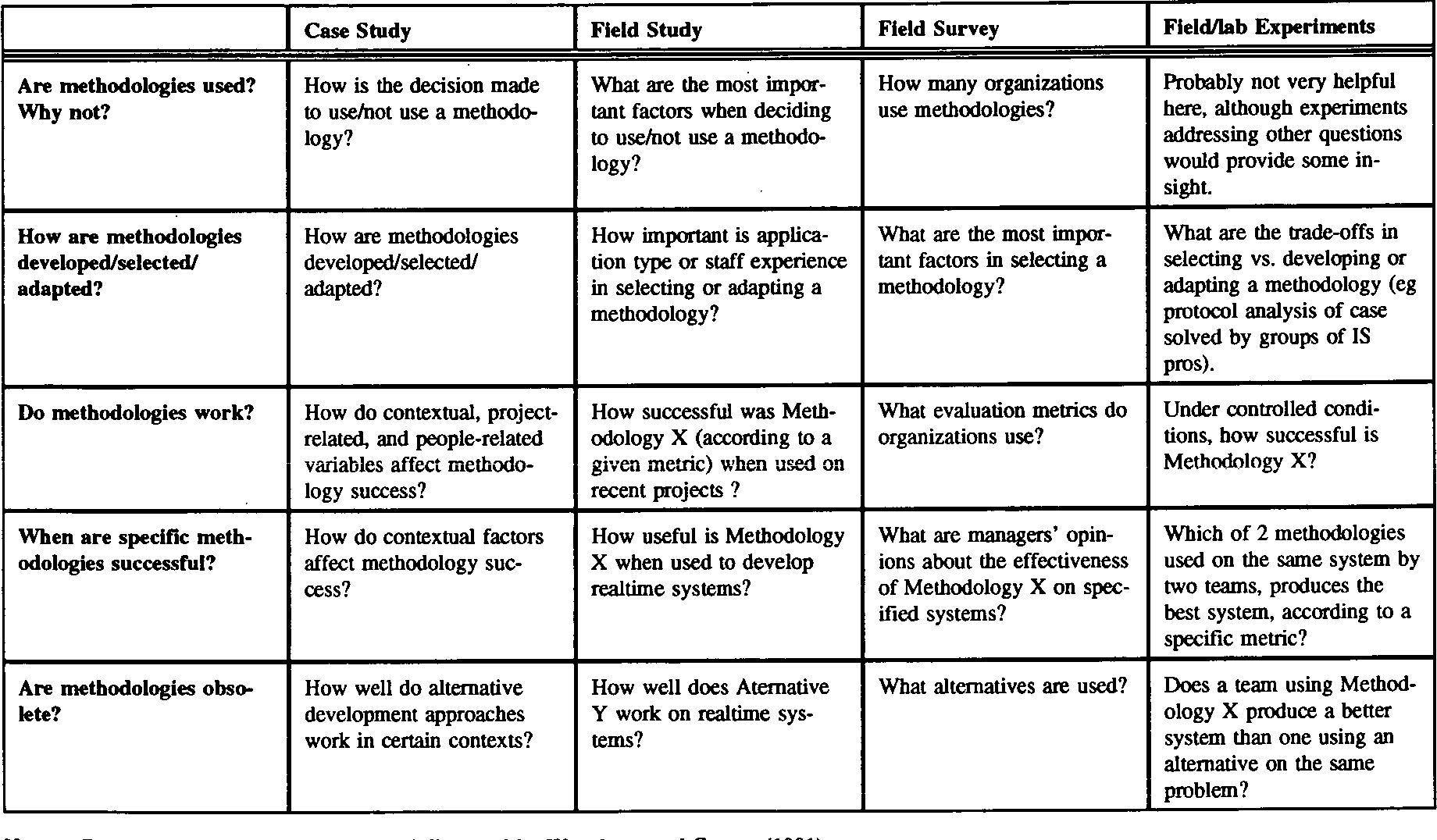
We have used two decision tree algorithms namely, Classification and Regression Tree and Chi-squared Automatic Interaction Detection in developing the proposed framework. In this article, we propose a DMAIC framework, driven by data mining techniques for defect diagnosis and quality improvement where historical and online process data can be effectively utilised. Under such practical constraints, it is desirable to apply DMAIC using online process data under day-to-day production situations or with little changes in process settings without compromising production. Further, there are many small and medium scale enterprises that cannot afford to conduct DOE.
#Example of kaizen in foundry Offline
But, DOE is an offline activity requiring time and other resources for conducting experiments and analyses. Statistical Design of Experiment (DOE) is used in the ‘Improve’ stage for obtaining optimal process settings for significant variables contributing towards quality improvement. Six Sigma Define-Measure-Analyze-Improve-Control (DMAIC) methodology has been widely used across industries as the best systematic and data driven problem solving approach for quality improvement. In this paper, it deals the various aspects of a systematic approach to understanding and development of quality cost system in cast iron foundries. Any reduction in the scrap and rework also positively influences the environmental impact of our industry. It will also encourage foundries to develop systems to measure process parameters relating to the defects that occur in the foundries and pool the resources of domain experts. The approach taken by this paper is expected to motivate the foundries to use a standard classification system to describe undesirable casting artifacts for more effective failure analysis. Any attempt to reduce these costs is an immense benefit to the foundry industry.
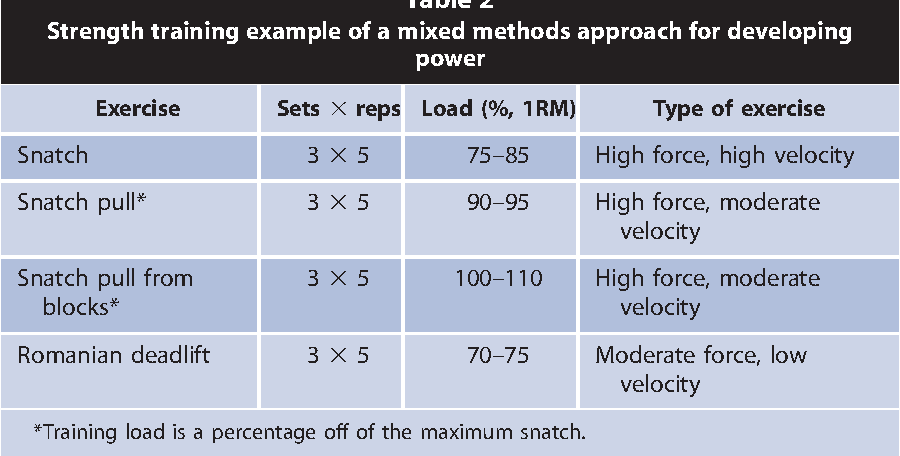
Quality costs in a foundry can vary between 3% and 15% of the total sales volume. Internal and external failure costs contribute to over 70% of the total quality costs in foundries. Also, there is a need for developing a database of solutions for eliminating undesirable casting artifacts. There is a need for an organized system of collecting information on the process parameters relating to the potential casting defects. Most of the foundries have no precise knowledge of the main causes of rejection because they fail to maintain a satisfactory quality control system. Keeping rejection to a bare minimum is essential to improve the yield and increase the effective capacity of the foundry unit.

The rejected casting can only be re-melted and the value addition made during various processes such as melting, moulding, fettling and heat treatment, etc is lost irrecoverably. However, in most foundries a substantial proportion of rejection result from lack of shop-floor supervision and technical control, and the use of poorly maintained and inadequate equipment. All foundry processes generate a certain level of rejection that is closely related to the type of casting, the processes used and the equipments available. In addition excessive rejection reduces yield, wastes valuable raw materials and involves management time in problem solving. High casting reject levels, both internal and customer returns have a considerable adverse effect on productivity, delivery performance, customer satisfaction and employee moral. The casting process is hindered by the occurrence of various defects. Cost-effectiveness does not mean a strategy that saves money and just because a strategy saves money doesn't mean that it is cost-effective. In the present global scenario of recession and high competitiveness among the foundry industry, cost effectiveness has a crucial role to play in determining the edge of one over the other and the industry as a whole. In the manufacturing sector, metal casting industry is one of the basic, principal and most important industries.
